Composite Fatigue Testing: Evaluating Long-Term Durability of Advanced Materials
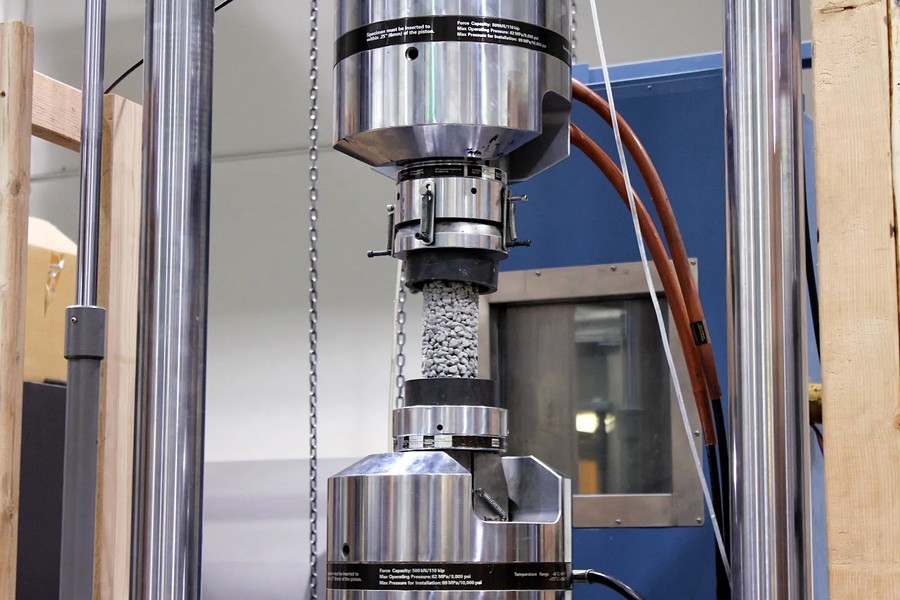
Composite materials, such as carbon-fiber-reinforced plastics (CFRP) and glass-fiber-reinforced composites (GFRP), are widely used in aerospace, automotive, and marine industries due to their high strength, low weight, and corrosion resistance. However, like any material, composites are susceptible to fatigue failure under cyclic loading. Composite fatigue testing is essential to understand the material’s behavior under repetitive stress and to predict its lifespan.
Understanding Fatigue in Composites
Fatigue failure in composites is a complex phenomenon due to the material’s heterogeneous nature. Unlike metals, which fail through surface cracks, composites can experience:
- Matrix cracking: Cracks form within the polymer matrix due to repeated loading.
- Fiber breakage: The reinforcing fibers can break, leading to loss of mechanical strength.
- Delamination: Separation occurs between different layers of the composite.
These failure modes can interact and accelerate the material’s deterioration, making fatigue testing critical in predicting long-term performance.
Purpose of Composite Fatigue Testing
Composite fatigue testing aims to:
- Determine the number of cycles the material can endure before failure.
- Identify failure mechanisms and how they propagate under cyclic stress.
- Provide data for designing safer, more reliable products.
Types of Composite Fatigue Testing
- Tension-Tension Fatigue Testing
The composite is subjected to repeated tensile loads to measure how it responds to stretching forces over time. - Compression-Compression Fatigue Testing
This test applies compressive forces repeatedly to study how the material resists crushing loads. - Flexural Fatigue Testing
The composite is bent repeatedly until it fails. This is common for testing components like aircraft wings and automotive body panels. - Thermal Fatigue Testing
Simulates conditions where the material experiences fluctuating temperatures along with mechanical stress.
Key Factors Affecting Fatigue Life
- Material Composition
The type of fibers, matrix, and their bonding quality significantly impact fatigue resistance. - Load Conditions
High-stress levels, loading frequency, and load direction can shorten the composite’s lifespan. - Environmental Conditions
Exposure to moisture, chemicals, or UV radiation can degrade the material and accelerate fatigue failure. - Manufacturing Quality
Defects during manufacturing, such as voids or weak bonds, can create stress concentration points.
Testing Methods
- Constant Amplitude Loading
The composite is exposed to a fixed cyclic load. This test is ideal for comparing fatigue life under known conditions. - Variable Amplitude Loading
Real-world conditions are simulated by applying varying cyclic loads. - Non-Destructive Fatigue Monitoring
Techniques such as acoustic emission and thermography are used to monitor internal damage during testing without destroying the sample.
Applications of Composite Fatigue Testing
- Aerospace Components
Fatigue testing ensures that structural components, such as fuselage panels and wing sections, withstand long-term cyclic loading. - Automotive Parts
Lightweight materials used in high-performance cars undergo fatigue testing to ensure durability under road vibrations and loads. - Wind Turbine Blades
Blades made of fiberglass or carbon fiber composites are tested to endure millions of loading cycles from wind forces.
Conclusion
Composite fatigue testing is a crucial step in ensuring that advanced materials meet the demands of long-term use. By understanding how composites respond to cyclic stress, engineers can design safer, more efficient products and prevent costly failures in critical applications.