Plant logistics: Linking material flows and production processes
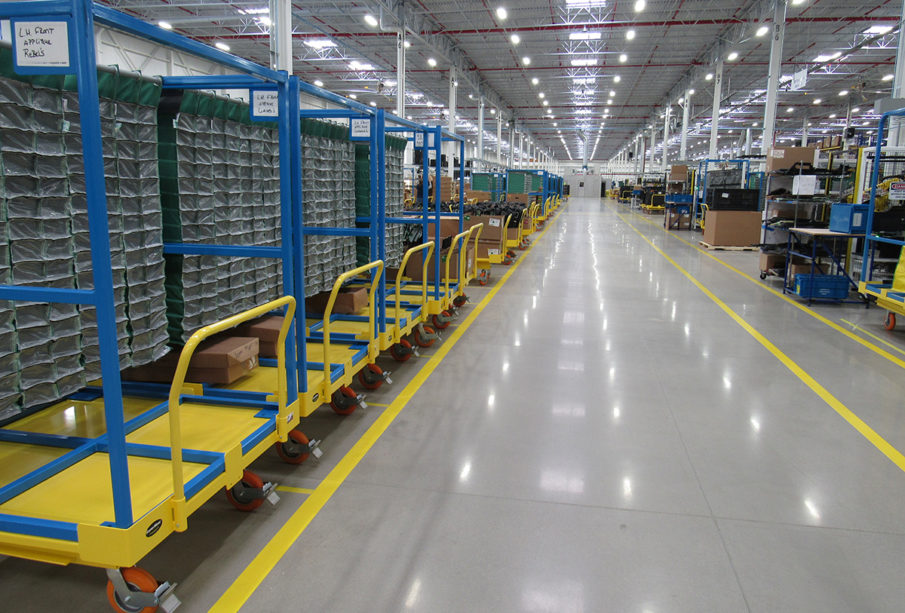
At some point or another, you must have come across the word logistics. It simply refers to the seamless synchronization of diverse operations. This collaboration can now include everything from commodities handling and transit through purchasing, packaging, and storage.
However, in order to have a complete picture of the full shipping process, you must understand what happens to materials within the plant. This is where plant logistics enters the picture.
Here’s everything you need to know about in-plant logistics to increase customer value.
What is plant logistics?
The transportation of components, raw materials and sub-assemblies within a company’s production plant is referred to as in-plant logistics. Goods (typically semi-finished goods) are carried from storage units to a facility where full production will take place in this mode of transportation (finished goods). In-plant logistics also entails transporting finished items to a location where they can be sold or consumed quickly.
What is the need to use plant logistics?
When a firm’s internal logistics system is effective, it aids in determining the overall delivery time; this includes transportation of commodities and their handling. It gives you a complete picture of what happens to semi-finished items within a plant, from when they are received to when they are dispatched to the production line and the transportation of that finished item to a bonded or non-bonded extra space within a facility.
All of these operations are achievable with a solid in-plant logistics system in operation, which improves the company’s overall performance. A robust in-plant logistics system also makes the whole process nimbler, making supply chain management easier, faster and less expensive.
How is in-plant logistics important for the production process and linking material flow?
Good in-plant logistics can help your organisation increase revenue by creating a holistic situation for consumers and providing them with suitable information about product availability, cost, timeliness, and efficiency. The efficacy of an in-plant logistics system is determined by how successfully you manage your plant’s activities from the inside out, beginning with raw material intake and ending with customer information. DHL’s expertise in global logistics come helpful in this situation.
DHL’s crew assists in the movement of raw materials, parts and sub-assemblies to and from stocking points for processing into completed goods, as well as moving finished goods out to the factory gate. What’s more is, they improve this process by delivering the relevant parts to the line-side for use in a production or sub-assembly item. This ensures that the correct parts are delivered to the manufacturing line in the correct order and at the appropriate time.
By delivering supplies directly to the installation site, lead times and stocks are saved, while productivity is boosted. This way, customer requests are addressed while still generating considerable profit for the company.
Overall, the major goal of in-plant logistics is to ensure that the customer is completely satisfied by focusing on the product order and delivery time. In short, time critical logistics is very important for in-plant logistics. Not just that, it also refers to the availability of items to a greater range of individuals, hence increasing consumer value. The results of this process are used to assess and redefine standard operating procedures, explore transportation, redesign time and cost reductions, and optimise warehouse management for maximum efficiency.
Therefore, if you too want your in-plant logistics system to be efficient and safe, get in touch with the experts at DHL.